When it comes to Operating Procedures, how detailed the procedure needs to be has always been an industry debate. Of course, the answer will depend on who you are; an operator or a process engineer. This is also the most common question when discussing the PSM operator procedure element during PSM Compliance Training. The answer is simple, the procedure needs to be as detailed as possible! If you ask the operator if they use the operating procedures as part of their daily duties or just refer to them as needed during an interview, the overwhelming majority response is to just refer to them as needed. If a well-trained operator is referring to a procedure only when needed, they better be well detailed. Secondly, the new operator MUST be trained on the operating procedures, and they should be a major source of their operations training. If we rely on seasoned operators to provide on-the-job training of new operations, then you can expect there to be operational deviations as compared to the written operating procedures. We all have bad habits and without good detailed operating procedures, bad habits become operational in short order. Your operating procedures may currently lack the sufficient detail needed, but it is never too late for “continuous improvement”. To begin, no matter the process type, have your most experienced operator start to add the detail. Let your lesser experienced operators review the more detailed procedures allowing them to learn the detail, ask questions, and receive feedback. You will be surprised what you learn when you start detailing out a procedure. More importantly, detailed procedures will avert operational errors and an incident. In the next part of this series, I will address the various operational phases that are required, common errors, and best practices to make your procedures a vital part of safe operations.
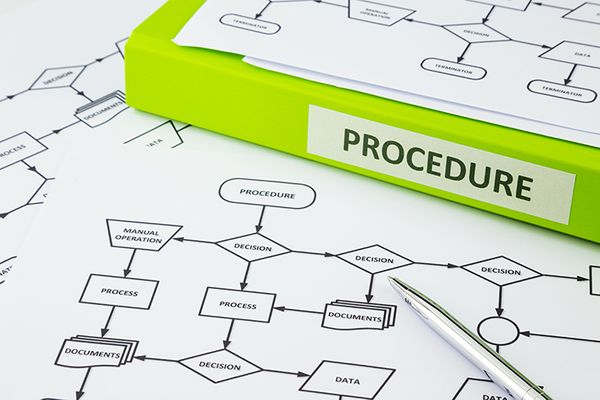
Operating Procedures – Part 1
Ric Hartung