In the last article regarding Management of Change, we discussed the three simple questions that can be asked to determine if a proposed change must be handled through your formal change management system, or if it is a replacement in kind. Assuming a change is not a replacement kind, a lack of a well-defined management system is where, in most cases, we see things go in the wrong direction from beginning to end. Most have a process for determining if a change requires an MOC, and if so, will also have a process of getting the MOC approved, Engineering Design process, conducting a PSSR, and how the MOC is closed. What occurs between the approval of MOC and conducting the PSSR is most critical for having a robust and effective management of change system. If your management system involves attaching documents to a MOC document, then you can expect to have failures and gaps in your system. For example, if you go back to the original design, EACH component on your P&IDs must have process safety information readily available. This information is best maintained in equipment files. In the old days, this was unwieldy paper files which were difficult to maintain current and accurate, but now these files can be maintained electronically, making the process easier and help to ensure that the PSI information is accessible to all. When a change takes place, each component equipment file that is affected by the change, must be updated to reflect the change, otherwise, your PSI becomes inaccurate leading to potential process safety incidents and events. Then, your PSSR should be more of a process of making a final check to ensure all PSI has been updated and reflects what is to be changed, health and safety reviews have been completed and action items resolved, procedures written, and training conducted, and the process is ready to receive chemicals or startup. It should not be a mad scramble at the end if your change management system addressed all the little things that need to take place before the PSSR is completed. If we find items that have not been completed at the time the PSSR is conducted, it is more than likely because we have issues with our management system that need to be resolved. Good checklists help to identify that we have done everything prior to startup. If you have ever flown, we trust that the pilots are following known safety protocols which include “checklists”! Use the checklist to help ensure we do not forget important protocols. Train and teach others to ensure continuous improvement.
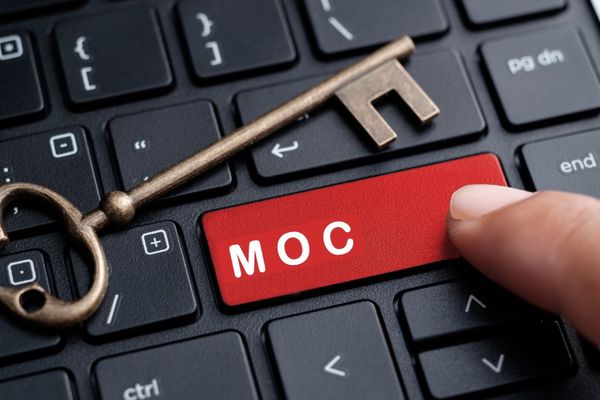
Management of Change (Part 3: A Change Management System)
Ric Hartung